Celková efektivnost zařízení (CEZ), anglicky Overall Equipment Effectiveness (OEE), je kvantitativním ukazatelem efektivnosti výrobních zařízení. Poskytuje měřitelné srovnání efektivnosti jednotlivých výrobních zařízení i celých výrobních podniků. Zahrnuje v sobě více složek ovlivňujících celkovou efektivnost, které lze samostatně vyhodnotit a použít k eliminaci nalezených ztrát (organizace, výkonu a kvality).
EFEKTIVITA NEBO EFEKTIVNOST?
Pojďme se nejprve podívat na pojmy „efektivita“ a „efektivnost“. Tyto pojmy se často zaměňují a i v rámci jednoho textu je autoři často střídají a používají coby synonyma. Jejich význam však není stejný. Efektivita (eficiency) představuje účinnost (obecně poměr mezi přínosem nějaké činnosti a náklady na ni vynaloženými), zatímco efektivnost (effectiveness) představuje účelnost, smysluplnost (vztah mezi stanoveným cílem a následkem).
Tradiční pojetí TPM definuje OEE jako Overall Equipment Eficiency, tedy celkovou efektivitu zařízení. Novější pojetí však OEE vidí jako Overall Equipment Effectiveness, tedy celkovou efektivnost zařízení. V dalším textu budeme pod zkratkou OEE rozumět Overall Equipment Effectiveness.
CELKOVÁ EFEKTIVNOST ZAŘÍZENÍ
Ukazatel Celkové efektivnosti zařízení (OEE) vytvořil v 60. letech Seiichi Nakajima ze společnosti Nippon Denso. Na konci 80. let se tato metodika dostává do povědomí díky rozšíření TPM. V polovině 90. let je pak aplikována v oblasti výroby polovodičových součástek za účelem zvýšení produktivity výrobních zařízení. Postupně metodiku přijala i ostatní odvětví průmyslové výroby.
Základní myšlenka metodiky spočívá ve vztahu:
OEE = Užitečný čas zařízení / Disponibilní čas zařízení,
kde:
- Užitečný čas zařízení – doba, kdy zařízení vyrábí shodné výrobky
- Disponibilní čas zařízení – doba, kdy by mělo zařízení vyrábět
Rozdíl mezi užitečným časem a disponibilním časem je dán mírou využití, výkonu a kvality. Nejčastější vyjádření vztahu pro výpočet OEE používá právě tyto tři ukazatele:
OEE = Availability x Performance x Quality,
kde
- Availability (dostupnost, využití) – poměr mezi výrobním časem a disponibilním časem
- Performance (výkon) – poměr mezi čistým výrobním časem a výrobním časem
- Quality (kvalita) – poměr mezi užitečným výrobním časem a čistým výrobním časem
Pro praktický výpočet uvedených ukazatelů se používají následující definice a vztahy:
Availability
Poměr mezi výrobním časem a disponibilním časem. Výrobním časem se myslí doba, kdy je zařízení v chodu. Disponibilním časem se pak myslí očekávaná doba chodu zařízení. Pro výpočet se používá vzorec v tomto tvaru:
Availability = Operating Time / Loading Time,
kde
- Operating Time – skutečná doba běhu zařízení
- Loading Time – očekávaná doba běhu zařízení
Performance
Poměr mezi skutečným výstupem a plánovaným výstupem. Pro výpočet se používá vzorec v těchto tvarech:
Performance = Total Output / Potential Output,
Performance = (Total Output * Ideal Cycle Time) / Operating Time,
kde
- Total Output – celkový počet vyrobených kusů
- Potential Output – plánovaný počet vyrobených kusů
- Ideal Cycle Time – plánovaná délka cyklu (výroby jednoho kusu)
- Operating Time – skutečná doba běhu zařízení
Quality
Poměr mezi výstupem kvalitních výrobků a výstupem všech výrobků. Pro výpočet se používá vzorec v tomto tvaru:
Quality = Good Output / Total Output,
kde
- Good Output – počet vyrobených kvalitních kusů
- Total Output – celkový počet vyrobených kusů
PŘÍKLAD VÝPOČTU OEE
Podívejme se na příklad konkrétního výpočtu OEE:
- Zařízení běžící ve třísměnném provozu má definován disponibilní čas: 22 hod a 50 min
- Zařízení bylo ve skutečnosti v běhu: 16 hod 4 min a 29 s
- Zařízení během této doby vyrobilo: 2000 kusů
- Z toho shodných kusů bylo: 1970 kusů
- Předepsaná délka cyklu je: 28,3 s
Availability = Operating Time / Loading Time
Availability = 16,075 hod / 22,83 hod = 0,704 = 70,4 %
Performance = (Total Output * Ideal Cycle Time) / Operating Time
Performance = (2000 * 28,3 s) / 16,075 hod = 0,979 = 97,9 %
Quality = Good Output / Total Output
Quality = 1970 ks / 2000 ks = 0,985 = 98,5 %
OEE = Availability x Performance x Quality
OEE = 0,704 * 0,979 * 0,985 = 0,679 = 67,9 %
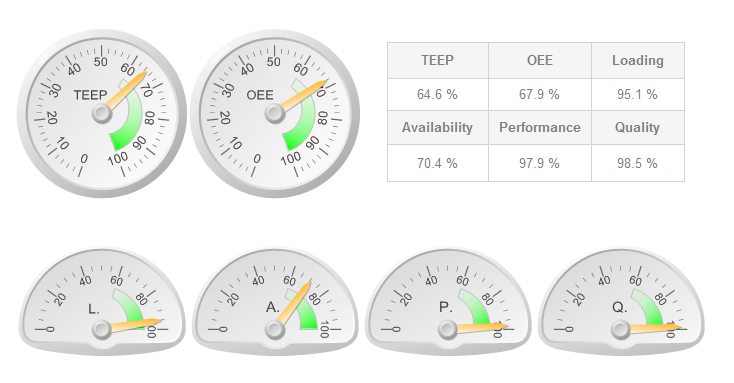
Uvádí se, že špičkové společnosti po úspěšné realizaci TPM dosahují OEE na úrovni 85%. Většina výrobních společností však dosahuje OEE na úrovni asi 60%. Je však nutné brát v potaz, jak a na základě jakých dat bylo toto číslo vypočítáno. Důležitou roli hraje kvalita a způsob sběru dat. Více viz kapitola Nástroje OEE.
ZTRÁTY OEE
OEE je klíčovým nástrojem TPM (Total Productive Maintenance) sloužícím k redukci a eliminaci tzv. „6 velkých ztrát“ (The Six Big Losses), které omezují produkci.
Šest velkých ztrát je rozděleno do tří základních oblastí:
Ztráty z prostojů
- Poruchy zařízení
- Seřizování a nastavování
Ztráty na výkonu
- Nečinnosti a krátké přestávky
- Redukce rychlosti
Ztráty na kvalitě
- Neshody a opravy
- Ztráty při rozběhu
Pokud do analýzy ztrát zahrneme i odvozený ukazatel TEEP, pak získáme ztráty dané organizací výroby. Tyto ztráty jsou způsobené odstávkami, na které není plánována výroba (jednosměnná či dvousměnná výroba, dovolené, svátky, …).
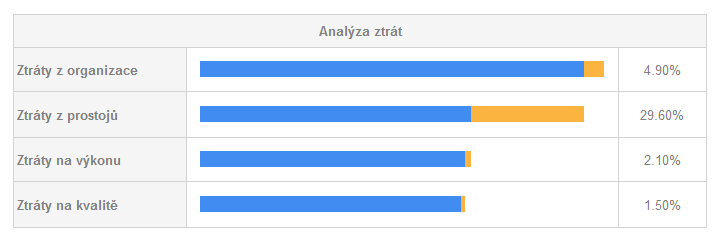
Analýzou ztrátových oblastí bychom měli být schopni identifikovat příčiny a zdroje ztrát. To nám umožní najít cesty ke zvýšení efektivnosti využití strojů a zařízení.
NÁSTROJE OEE
Důležitým aspektem pro výpočet ukazatelů OEE je sběr vstupních dat. Strategie sběru dat se může pohybovat od primitivních manuálních záznamů až po sofistikovaná automatizovaná řešení.
Manuální sběr dat je založen na papírových formulářích, do kterých obsluha výroby zapisuje události ovlivňující efektivitu výroby. Jedná se o zpětná hlášení z výroby (vyrobené kusy, neshodné kusy, …), příčiny a délky trvání prostojů, důvody ztrát výkonu apod. Sofistikovaná řešení jsou pak založena na automatickém sběru těchto dat ze strojů, průběžné registraci obsluhy k prováděným činnostem, průběžném hlášení neshodné výroby a odchylkové výroby.
Rozdíl mezi manuálním a automatizovaným sběrem dat je především v následujících oblastech:
- Kvalita dat – data získaná manuálně obsahují úmyslné i neúmyslné chyby a nepřesnosti (dané prvotním zápisem obsluhou výroby nebo opisem do nadřazeného systému), nezohledňují krátkodobé prostoje a jejich pořizování zatěžuje obsluhu výroby a další administrativní pracovníky.
- Dostupnost dat – data získaná manuálně nejsou dostupná v reálném čase. Jsou pořizována převážně na konci směny a do nadřazených systémů se díky manuálnímu zadávání dostávají s dalším zpožděním.
Automatické sběry dat (ze strojů či elektronické registrace obsluhy) eliminují vznik chyb a nepřesností a poskytují data v reálném čase. Vyhodnocení OEE tak může být pořizováno pro ukončenou i probíhající výrobu.
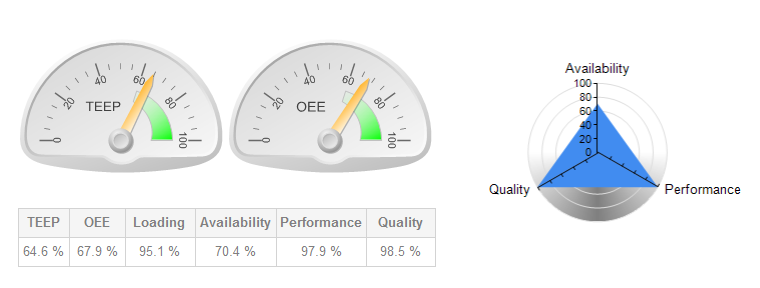
Součástí automatizovaných systémů OEE pak většinou bývají i nástroje pro vizualizaci, analýzu a reportování OEE výsledků. Takové nástroje by měly obsahovat funkce pro tvorbu vlastních customizovatelných reportů, agregační funkce, prostředky pro analýzu ztrát, souhrnné i detailní přehledy přes jednotlivé stroje až po celé výrobní podniky.
Pro vztažení ukazatelů OEE na celopodnikovou úroveň přicházejí v potaz odvozené ukazatele OAE, OPE a OFE, na které se podíváme v další kapitole.
ODVOZENÉ UKAZATELE TEEP, PEE, OAE, OPE, OFE, OTE, CTE
V reakci na nové požadavky hodnocení efektivnosti vznikly vedle OEE ještě další odvozené ukazatele. Některé z nich (TEEP, PEE, …) se pohybují na úrovni zařízení, zatímco jiné (OAE, OPE, OFE, …) rozšiřují OEE na úroveň podniku. Projděme si jejich základní charakteristiky:
TEEP – TOTAL EQUIPMENT EFFECTIVENESS PERFORMANCE
Nejznámější z odvozených ukazatelů TEEP (Total Equipment Effectiveness Performance) ve výpočtu zohledňuje plánované prostoje. Zatímco OEE kvantifikuje, s jakou efektivností je zařízení využito v rámci plánovaného času (plánovaných směn), TEEP posuzuje efektivnost zařízení vztaženou ke kalendářnímu času (tedy k 24 hodinám denně, 7 dnům v týdnu a 365 dnům v roce). Pokud by chod zařízení byl plánován na 24 hodin denně, 7 dnů v týdnu a 365 dní v roce, pak TEEP odpovídá OEE. TEEP lze vyjádřit vztahem:
TEEP = Užitečný čas zařízení / Kalendářní čas,
nebo:
TEEP = Loading x Availability x Performance x Quality = Loading x OEE,
kde
- Loading (dostupnost) – poměr mezi disponibilním časem a kalendářním časem
- Availability (využití) – poměr mezi výrobním časem a disponibilním časem
- Performance (výkon) – poměr mezi čistým výrobním časem a výrobním časem
- Quality (kvalita) – poměr mezi užitečným výrobním časem a čistým výrobním časem
Pokud se podíváme na uvedený příklad výpočtu OEE a doplníme ho o výpočet ukazatele TEEP, dostaneme tyto výsledky:
Loading = 22 hod 50 min / 24 hod = 0,951 = 95,1 %
TEEP = 0,951 * 0,704 * 0,979 * 0,985 = 0,679 = 0,646 = 64,6 %
PEE – PRODUCTION EQUIPMENT EFFICIENCY
Dalším odvozeným ukazatelem je PEE (Production Equipment Efficiency). Hlavní odlišnost tohoto ukazatele spočívá ve vahách dílčích ukazatelů (Availability, Performance a Quality). Zatímco u OEE mají všechny dílčí ukazatele stejnou důležitost, u PEE je důležitost dílčího ukazatele dána nastavenou vahou.
Způsob výpočtu PEE se dále liší dle typu výroby:
Diskrétní výroba
Pro diskrétní výrobu zůstávají dílčí ukazatele stejné jako v případě OEE, pouze jsou doplněny váhy jednotlivých ukazatelů:
PEE = (Availability)k1 x (Performance)k2 x (Quality)k3,
kde
- ki – váha ukazatele i, 0 < ki ≤ 1, ∑ki = 1
Kontinuální výroba
Pro kontinuální výrobu je vztah pro výpočet PEE definován jako:
PEE = (Availability)k1 x (Attainment)k2 x (Performance)k3 x (Quality)k4 x (PSE)k5 x (OU)k6,
kde
- ki – váha ukazatele i, 0 < ki ≤ 1, ∑ki = 1
- Availability – zohledňuje plánované prostoje a přibližně odpovídá ukazateli Loading z metodiky TEEP
- Performance – odpovídá ukazateli Performance z metodiky TEEP
- Quality – odpovídá ukazateli Quality z metodiky TEEP
- PSE – Product Support Efficiency zohledňuje transakční ztráty
- OU – Operating Utility zohledňuje ztráty z poptávky
V případě kontinuální výroby se předpokládá, že neexistují ztráty ze seřizování a proto se ve výpočtu PEE nezohledňují.
OAE/OPE – OVERALL ASSET/PRODUCTION EFFECTIVENESS
Ukazatele OAE (Overall Asset Effectiveness) a OPE (Overall Production Effectiveness) vycházejí z metodiky OEE. Byly navrženy tak, aby odpovídaly specifickým požadavkům různých odvětví, proto se v praxi vyskytují pod různými definicemi. Ze všech jmenovaných ukazatelů zahrnují největší spektrum kalkulovaných ztrát – používají se k identifikaci a měření všech ztrát spojených s celým výrobním procesem.
Pokud jde o aplikaci ukazatelů v průmyslu, mají oba stejný význam, liší se však v pojetí výrobních ztrát. OAE kvantifikuje výrobní ztráty dle výstupu, kdežto OPE dle času.
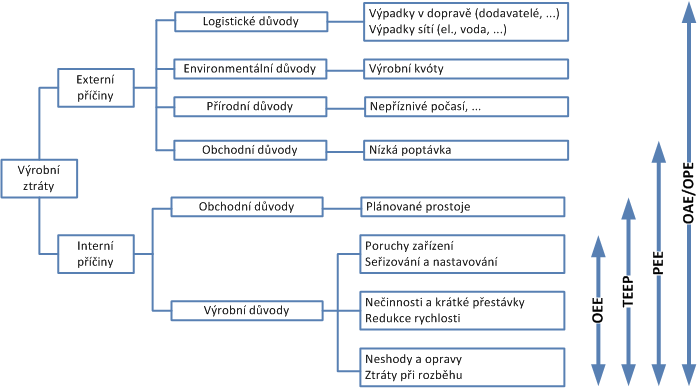
OFE – OVERALL FACTORY EFFECTIVENESS
Pro vyjádření efektivnosti vztažené na celý výrobní podnik slouží metodika OFE (Overall Factory Effectiveness). Pokud ve výrobě probíhá více výrobních kroků na více zařízeních, není možné na celopodnikové úrovni klasické OEE použít. Zatímco OEE se zaměřuje na efektivnost jednotlivých zařízení, OFE vyhodnocuje všechna zařízení dohromady. Do výpočtu zahrnuje vztahy a interakce mezi různými zařízeními a procesy.
Výrobní prostředí se skládá ze subsystémů, které lze rozdělit na 4 základní skupiny:
- Series (sériová, v řadě)
- Parallel (paralelní, souběžná)
- Assembly (spojení, montáž)
- Expansion (rozdělení, expanze)
Pomocí těchto 4 skupin subsystémů lze namodelovat celý výrobní provoz. Efektivitu jednotlivých subsystémů pak zkoumají metodiky jako OTE (Overall Throughput Effectiveness) nebo CTE (Cycle Time Effectiveness).
OTE vyjadřuje poměr mezi skutečným výstupem a teoreticky možným výstupem. Metodika je úzce spojena se simulačními technikami pro zvyšování produktivity výroby. CTE je pak poměrem mezi teoretickou délkou cyklu a skutečnou délkou cyklu.
Miroslav Patočka
Analytik systému MES PHARIS
UNIS, a.s.